Services
We Provide A Wide Range Of quality control Services
What Quality Inspections programs Do We Provide?
Our aim is to provide you quality control solutions for your business starting from the time the raw material leaves the supplier to the point that your finished product is shipped to the customer. 365Inspections provide multiple quality control inspections including:
We focus on each stage of the production. Consumer Product Inspection can be performed in different stages of Production cycle, we offer an Initial Production Inspection to ensure the necessary quality of the raw materials and that our client and the vendor understand the specifications. A second check called During Production Inspection is done when at least 20% of the run has been completed and a third check called Pre-Shipment Inspection when 80% are ready and packed. These certify that the Production is carried out according to the clients’ tailored stipulations, ensuring that any problems can be solved systematically. Inspectors can monitor the factory daily, weekly or as specified to guarantee competency through our Production Monitoring Service, sending you a final report on the same day of inspection. The final check is Container Loading Check to ensure the goods will reach their destination in excellent condition.
Pre-shipment Inspection (PSI): it is carried out when a minimum of 80% of the goods are ready and packed. The Inspection ensures that the Production is in accordance with the approval sample, product specifications, client’s requirement, purchase orders or letters of credit.
The main aspects checked for PSI:
– Quantity and packing details check.
– Marking and labeling check.
– Style, color, size & material check.
– Appearance and workmanship check.
– Function/ safety check.
– On-site testing that depends on the products (such as reliability test, assembly test, carton drop test, etc.)
Initial Production Inspection (IPI): This Inspection takes place at the early stage of Production and it aims to check the raw materials and to make sure that the customer’s specifications are well understood by the vendor.
The main aspects checked for IPI:
- Evaluate the production capacity and equipment in the factory, providing the estimated cargo ready date to client for reference.
- Check the quality control system in the factory.
- Audit production technique and make sure QC staff will be arranged.
- Check the quality and quantity of the raw material and main components that will be used in the products, foreseeing any possible problem and remind the factory accordingly, verifying the client’s requirement and product specification are being met early.
During Production Inspection (DPI): The Production is inspected when at least 20% of the order has been completed so as to ensure the contractual obligations of the order are met.
The main aspects checked for DPI:
– Evaluate the production status during the manufacturing process.
– Randomly inspect the finished samples on-site and compare with the client’s approval samples and production specification.
– Ensure the proper QC process being set up in production line and the defective products are being rejected by the factory QC.
– Provide corrective action to factory production management for defective products.
– Inspect the packing details and material.
Container Loading Check (CLC): It is carried out in the manufacturer’s warehouse or at the forwarder’s premises to check the products’ basic information, quantity, condition of package during loading and supervise the whole loading process to ensure the cargo is loaded into the container in its entirety and in a secure manner.
The main aspects checked for CLC:
– Record the weather, arrival time of container, container No., truck No.
– Check the condition of the container if there is any damage, hole, wet, abnormal smell, etc.
– Quantity check of goods loaded and check the condition of packaging (pallets/cartons).
– Randomly select and open some cartons to verify the goods as client’s specifications.
– Monitoring the whole loading process.
– Seal the container with the custom’s seal and record the No.
– Record the departure time of the container.
Production Monitoring (PM): Having an Inspector sent to the factory daily, weekly, or as the client specify of a certain period of time to receive a report after each Inspection on Production quality and process. In this service you will keep a safe pressure on your supplier.
The main aspects checked for PM:
– Report the production status and quality issues found in every visit.
– Randomly inspect the semi-products or finished products on all stages of production process and compare them with client’s approval samples and production specifications.
– Ensure that the proper quality control policy being maintained and implemented during production line and all the defective products are being rejected by the factory QC.
Provide corrective action to factory production management for defective products.
Our Factory and Social Auditing ensure that factories meet and maintain their ISO 9000, ISO14000 and SA8000 standards, including issues like production capacity, quality control system, hygiene, safety, local labor laws, and child labor policies. This will confirm that the factory is the right one for each client’s needs, offering exactly the standards that are needed at the correct production levels. You can rest assured, knowing that laws and ethics are being upheld and your company’s image maintained.
-Factory Audit: we will perform the audit according to ISO9000 and International Quality Standard. Our Certified Auditor will review the factory profile, organization, production capacities, machines, quality control system, and working conditions and facilities. This final report will help you to evaluate your supplier and confirm if the production capacity and quality can meet your production level.
-Social Audit: we will perform the Audit according to SA8000 and local laws and regulations. It’s important to know the laws and ethics are being upheld to maintain your product image and reputation. The Auditor will assess child and forced labor, health and safety, freedom of association, discrimination and discipline, working hours and compensations, and management systems.
Our lab testing utilizes International Certified Laboratories to ensure the testing is done right the first time at a reasonable price. Not only will we inform you of the necessary tests for your Product, the sample will be from your lot to preserve consistency.
Quality Standard
365Inspection uses the commonly recognized Acceptable Quality Level (AQL) standards as MIL-STD-105E (equals to ANSI/ASQC Z1.4, ISO 2859, NF06-022, BS 6001 or DIN 40080) to perform product inspections. This commonly used method is to measure and determine the maximum defective products found during inspection process from the selected sampling size. In the final report you will have all the data of quality issues to make an informed decision whether you accept or reject your production.
How to choose the sample size and acceptance number?
365Inspection default Acceptable Quality Level is II for a Standard Inspection. For your convenience, you can choose and set your Acceptable Quality Level through our online booking platform.
Let’s take a hypothetical Inspection of a Production with 10,000 pieces. In Table A, under the column level II, we get letter L.
According to Table B, we will inspect 200 pieces randomly. For AQL of 2.5, the maximum number of defective product should be no more than 10 pieces, otherwise the report will fail.
Table A
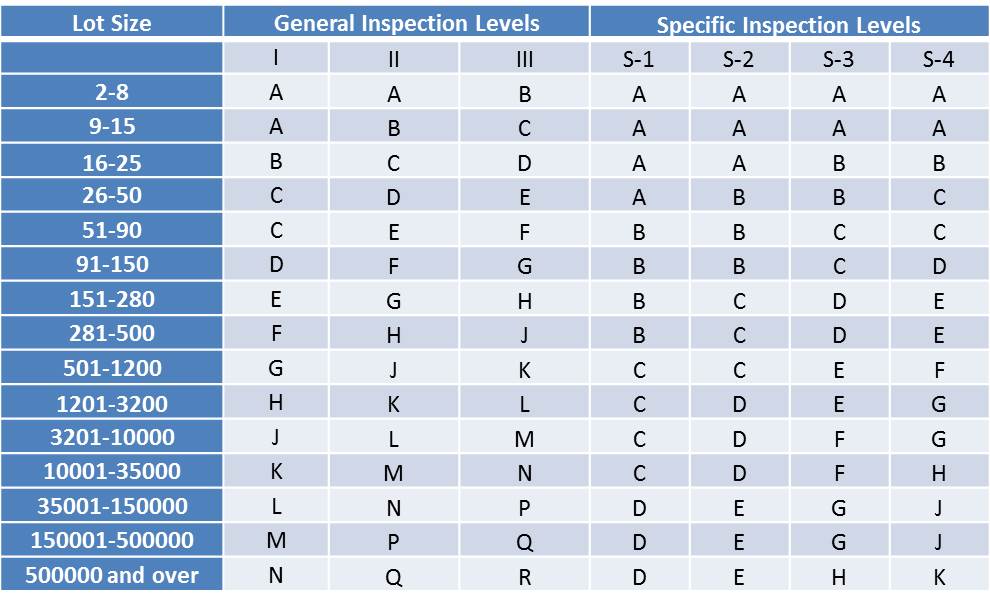
Table B
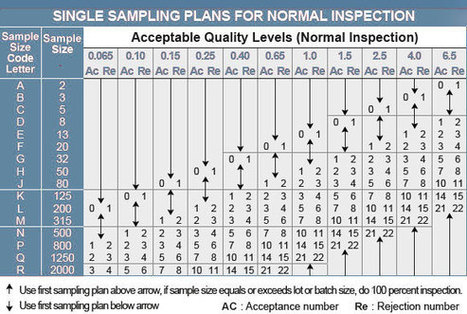